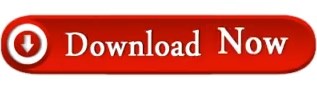

It is desired to specify the appropriate angle sections that will safely carry the anticipated loading using Eurocode design code (Specified steel grade S 275). The truss is made up of Howe Truss configuration spaced at 3m intervals. The skeletal structure of a roof system (18.0m long and 7.2m wide) is as shown in the Figure below. To illustrate this, a simple design example has been presented. Example on the Design of Steel Roof Trusses The flexural buckling in Eurocode 3 is achieved by applying a reduction factor to the compression resistance. In most truss members, only flexural buckling of the compressed members in the plane of the truss structure and out of the plane of the truss structure need to be evaluated. However, it should be noted that the architectural design of the building determines its external geometry and governs the slope given to the top chord of the truss.įor the design of a compression member in a roof truss, several buckling modes need to be considered. No tolerance is allowed between end wall top and rafter.For a good structural performance of roof trusses, the ratio of span to truss depth should be in the range of 10 to 15. "Rafters" should be supported by wall and hip rafter.Physical contact or joint between members is needed to detect support relations and complete load transfer.Profiles carrying loads from other members must be “Hip Rafters”, "Valley Rafters" or "Ridge Beams".Function property of the profiles which are transferring loads from covering material like sheeting to trusses must be "Rafters" or "Joists".Beam functionality is set to Main beam, beams should be supported by vertical bearing element, meaning column or bearing wall.Walls, beams, roofs, ceilings and floors can work as bearing components with some limitation. All objects are not working as bearing components. Trusses are supported by other objects in building model and the environment need to be completed before trusses are added. Step 1: Model walls, roofs, ceilings, floors and main beams
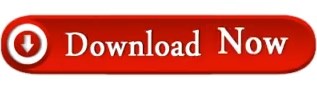